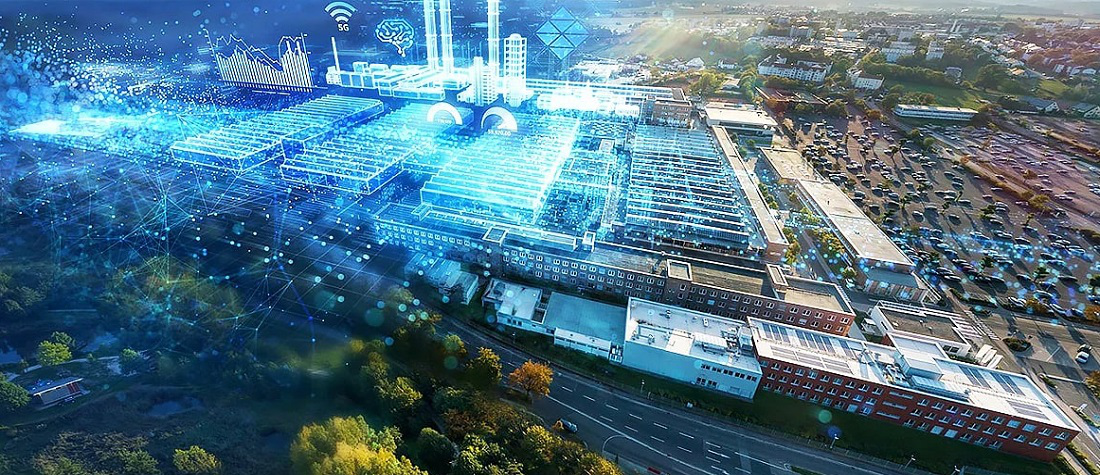
Digital twins
Every year, industrial technologies are becoming more complex and demanding. Modern production processes require high-precision solutions to increase efficiency, reduce costs and minimize risks. In this context, the technology of digital twins (Digital Twins) has become a revolution in industry, providing virtual copies of real objects and processes for their modeling and testing in a safe digital environment.
What is a digital twin?
A digital twin is a virtual model of a real physical object, system or process that is constantly updated with data from real objects in real time. This data can include information on temperature, pressure, vibrations and other parameters that are collected using sensors installed on the object.
A digital twin enables engineers and analysts to simulate and test various scenarios, analyze system behavior without having to interrupt or stop the operation of a physical object. This is used for gambling sites like Casino Joka online and is especially important for complex industrial systems such as oil refineries, aircraft engines or logistics networks.
How do digital twins work?
The principle of digital twins is the tight integration of physical objects and their digital models through sensors and data collection systems. Here are the main stages of work:
- Data collection. Data is collected from physical objects in real time through sensors. This can be temperature changes, vibration levels, resource consumption and many other parameters.
- Analysis and modeling. The digital model of the object is updated with this data and allows for analysis and simulation of various situations. For example, you can test how changes in equipment settings will affect its operation, or predict possible breakdowns based on the data received.
- Optimization and forecasting. Based on data analysis, you can optimize the operation of the production process or equipment. A virtual twin can also predict potential problems and help plan maintenance to prevent failures.
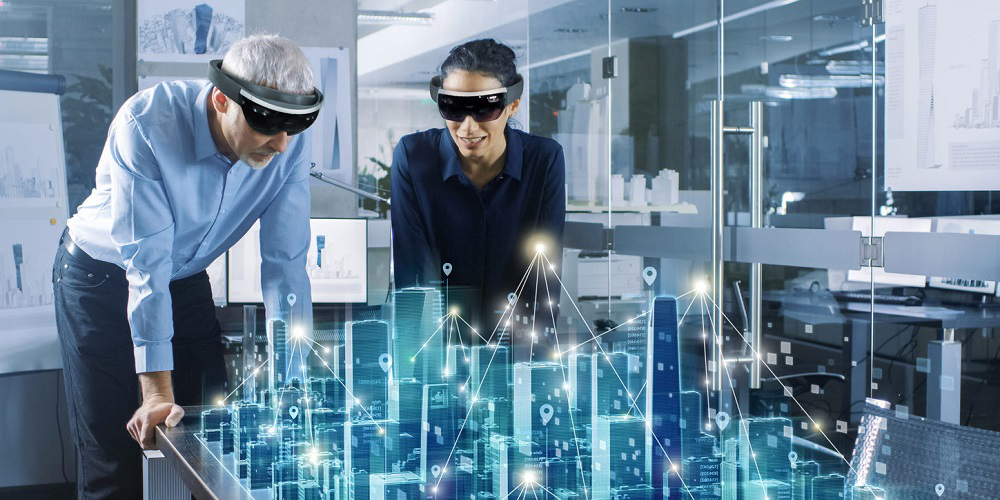
Benefits of using digital twins
Using digital twin technology brings significant benefits at different stages of production processes:
- Optimization of productivity. Digital twins allow you to model and analyze production processes, identify bottlenecks and optimize parameters to improve productivity without stopping real equipment.
- Increased reliability and safety. A continuous monitoring system allows you to identify problems at an early stage and take timely measures, which increases the safety of production processes.
- Scenario modeling. One of the key benefits is the ability to test different scenarios. For example, you can model how new equipment operating parameters will affect its performance, or how a change in the production schedule will affect the final results.
Examples of digital twin application
Today, digital twin technology is actively used in various industries, including:
- Automotive. Companies such as Tesla and BMW use digital twins to model the operation of car systems and improve their reliability and efficiency.
- Energy. In energy companies, digital twins are used to control and optimize the operation of power plants, which helps reduce energy consumption and improve system reliability.
- Aircraft industry. In aviation, digital twins are used to simulate the operation of engines and flight control systems, which allows testing new technologies and reducing maintenance costs.
- Gambling: In gambling control systems, digital twins are used to test slot machines for payouts. Thanks to this, the Casino Joka online project has the appropriate standards for gambling.
- Medicine. In healthcare, digital twins help simulate the operation of medical devices such as pacemakers or prostheses, which improves their efficiency and safety.
Digital twins have become an important element of modern manufacturing, providing businesses and industrial enterprises with new tools to improve productivity, safety, and reliability. The ability to test and optimize production processes in a virtual environment opens up new horizons for various industries, reducing costs and increasing efficiency.